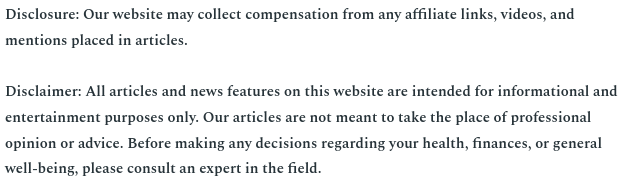

All types of foods are packaged along assembly lines nowadays, and, because of the very real possibility of contaminants being missed during the packaging process, a food metal detector is used as an important step in the operation. A food metal detector is used to identify specific impurities or toxins that could be hidden within the food itself. This type of metal detector looks for explicit forms of metallic contaminants within the product that could potentially be harmful to the consumer, which would, in turn, be harmful to the company. Every year one out of six people in the United States becomes sick as a result of some type of disease contracted from something they ate. Of these 48 million people, 128,000 will end up in the hospital, and another 3,000 will lose their lives. The three particular types of toxins detected by a food metal detector are stainless steel, ferrous, and non ferrous contaminants.
After traveling along the assembly line, foods and other products that are shown to comply with regulations will be industrially packaged by a form fill seal machine. These packaging machines will seal the product into food grade vacuum pouches and seal them with heat. Before sealing, any air within the packaging will be removed, and, when completely free of air, a heat bar will be laid across the top of the bag for safe sealing.
When the packaging process is finished, the sealed bags of product go through either automatic or manual checkweighers that will measure and weigh the finished product. These checkweighers are used to ensure that every package complies with specifications. Checkweighers are sometimes called in-motion scales or conveyer scales. These machines are made to ensure that 100% of every product is weighed right down to the ounce. Every number must be exact in order for each packaged product to be placed on the truck for delivery. A checkweigher will remove any packages that are overweight, which will save the company a lot of money in the long run. On the other side of this coin is the fact that there have been entire truck loads of product that were rejected simply because one package was underweight. This can be a devastating blow for a company that depends upon the sale of their product to keep them going.
These days more and more people are turning to products, including the product’s packaging, that are tuned in to contributing to a safe environment. Recycling has become a big part of life for an estimated 60% of people in the United States, and it is something that many people are very passionate about. This percentage of people are all able to connect with some kind of recycling program. It is now estimated by experts that for every pound of plastic packaging, there is a reduction of 1.7 pounds of wasted food.
Correct packaging, obviously, is one of those steps within the manufacturing of any product that is, although in the background, so important that it can make or break the distribution and sale of the product. Specifications are strict and must be cautiously adhered to.