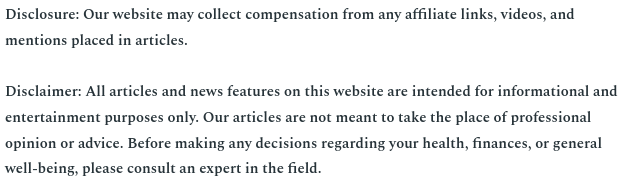

A tremendous amount of our food is pre-packaged. Packaging allows food to travel long distances safely and let’s us eat foods that we might otherwise have no access to. Food packaging materials and food packaging equipment have to be perfectly sterile and regularly inspected in order to ensure the quality and safety of all of this food. But even the safest, cleanest, and most regularly maintained machines are not enough. Once the food has been processed, it still needs to be inspected.
Each year, more then 48 million people in the United States get sick from some kind of food borne disease, and 3,000 die. While many foodborne illnesses are the result of eating fresh food that has not been properly cleaned or has turned, packaged food also must be kept safe. Because food is so often processed by industrial packaging machines with a minimum of human involvement, it is essential that food inspection systems be in place to make sure the food supply is safe. From the food metal detector to the food x-ray machine, here’s what food inspection tools are doing to keep us safe:
The Food Metal Detector
Since food is processed using machines, it is possible for metal to get into the food supply. A food metal detector is the most common method for checking that this does not happen. There are three kinds of metal contaminants that the average food metal detector can sense. They are able to find stainless steel, nonferrous, and ferrous metals. The typical food metal detector can find bits of stainless steel as small as 2.5 to 3.5 mm.
The first food metal detector was patented in the 19th century. Today’s metal detectors use microprocessors to ensure reliability and allow the machines to be integrated with other machines. A food metal detector is typically capable of examining both wrapped and unwrapped food either fresh or frozen, and in a variety of packaging. There are several different types of metal detectors, and each has advantages in certain applications.
Food X-ray Machines
Food x-ray machines are able to detect particles as small as 1.5 mm, improving food safety. When used in conjunction with a food metal detector, X-ray food inspection can ensure that packaged products are safe and healthy. The x-ray and inspection systems also help to protect individual brands, since customers depend on quality brands to always provide safe and healthy food. The x-ray inspection systems are able to find contaminants like glass, metal, stone, bone, and plastics. Another advantage of the x-ray inspection system is that it can do an in-line quality check as it checks for food safety. These systems are able to count components, measure mass, inspect the integrity of packaging seals, and other chores.
Food Inspection Innovations
As new methods of packaging as well as new foods and combinations of foods regularly enter the market, the food inspection industry is always in need of new ideas and innovations to provide low cost, but effective, food inspection. New systems are currently being developed that will allow inspectors to detect items that could not be seen in the past and to analyze unusual and irregularly shaped packages. New systems will also allow for remote access and integrate with networking programs. This will allow more manufacturers to keep a closer eye on their own food inspection. It also means that the Food and Drug Administration and other food inspection bodies will be able to login and monitor inspections in real-time.
Modern forms of food packaging are essential to twenty-first century life, but no packaging system is worth any risk to human health. Food inspector tools and systems are a reliable way of ensuring that the American food supply is safe.